SS / Duplex & Super Duplex 45 - 90 DEGREE ELBOW, LR/SR
Home - SS / duplex & super duplex - SS / duplex & super duplex Seamless Buttweld Fittings - SS / Duplex & Super Duplex 45 - 90 DEGREE ELBOW, LR/SR
SS / Duplex and Super Duplex 45-degree and 90-degree Elbows (LR & SR)
EBY Fasteners offers a range of 45-degree and 90-degree elbows in stainless steel (SS), duplex, and super duplex variants, meeting diverse industry needs. These LR and SR elbows excel in corrosion resistance, making them ideal for critical applications in oil and gas, marine, and petrochemical sectors
Crafted from high-quality stainless steel, EBY’s SS elbows ensure durability and efficiency in pipelines and structural setups, maintaining flow integrity. For more demanding environments, their duplex and super duplex elbows provide enhanced strength and resistance to corrosion, meeting stringent requirements for offshore platforms and chemical plants
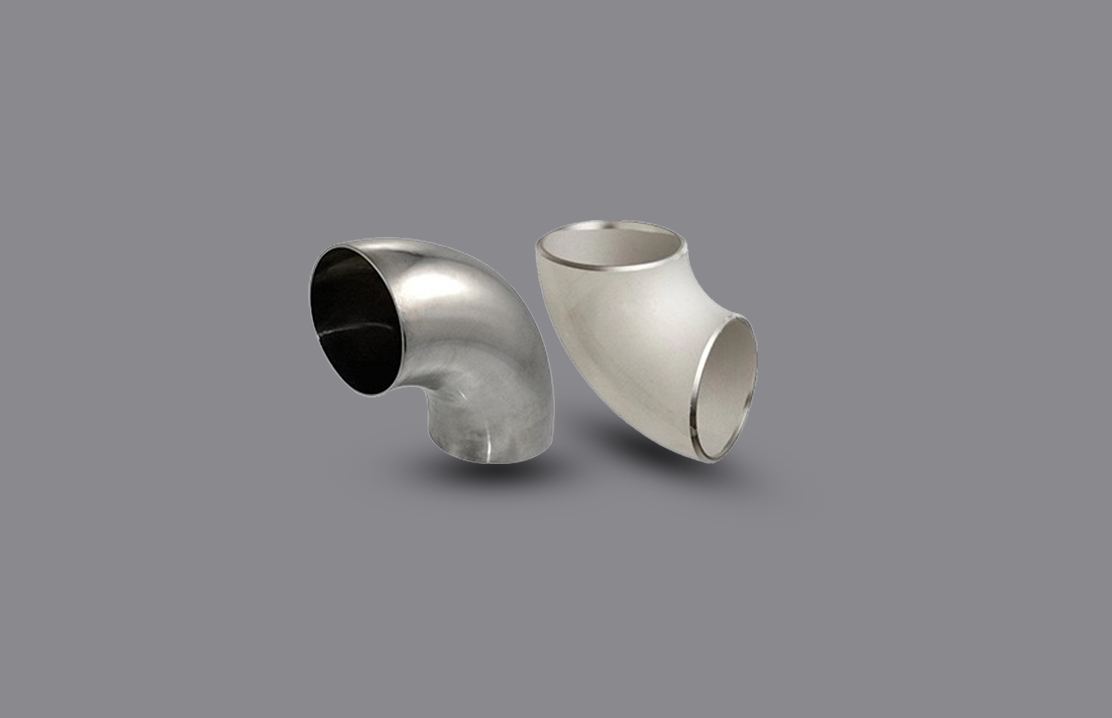
EBY Fasteners’ expertise guarantees reliable, high-performing elbows tailored to specific project needs, ensuring durability and compatibility across various industrial applications
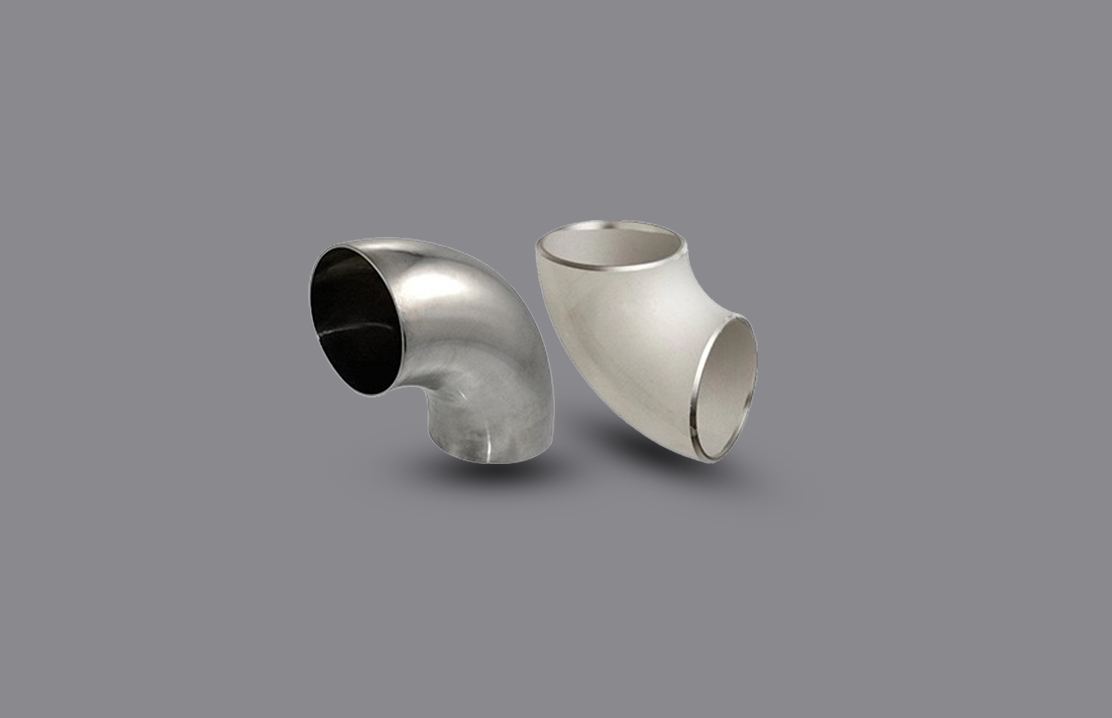
EBY Fasteners’ expertise guarantees reliable, high-performing elbows tailored to specific project needs, ensuring durability and compatibility across various industrial applications
- ASTM A815 / ASME SA815 : This standard is crucial for ensuring that your elbows, regardless of material, meet dimensional requirements, acceptable tolerances, and undergo appropriate testing. Compliance guarantees compatibility within your piping system and reliable long-term performance.
- S31803 / S32205 : Duplex 2205 is the "workhorse" of the duplex stainless steel grades. It offers a significant step up in strength and corrosion resistance compared to basic stainless steels like 304 or 316. This makes it versatile for many industries, including chemical processing, desalination, and even marine environments.
- S32750 : Super duplex 2507 takes corrosion resistance to another level and is commonly used in offshore oil and gas platforms, demanding chemical processing applications, and seawater systems. Its high strength contributes to its suitability in high-pressure environments.
- S32950 : This super duplex grade is less common than 2507 but boasts even higher resistance to specific types of acids and chloride-induced pitting corrosion. It's a niche choice for extremely aggressive environments.
- 304/304L : These are basic, versatile stainless steels. 304L is the low-carbon version offering slightly better weldability.
- 316/316L : Enhanced corrosion resistance (mainly chlorides) due to molybdenum. 316L is the low-carbon version for improved welding characteristics
- Standards : Standards play a crucial role in the manufacture of SS, duplex, and super duplex elbows. Adherence to standards such as ASTM and ASME guarantees dimensional accuracy, reliability, and compatibility within piping systems.
- Materials : For stainless steel, common grades include 304/304L and 316/316L, with relevant standards being ASTM A403 or A815. Duplex stainless steel elbows often utilize grades like 2205 (UNS S31803/S32205), while super duplex elbows rely on grades such as 2507 (UNS S32750). ASTM A815 is the key standard for both duplex and super duplex fittings.
- Size : Elbows come in a wide range of sizes and dimensions. Diameters can range from smaller process lines (1/2") to large industrial piping (up to 48" or even larger custom sizes). Wall thickness is critical and aligns with ASME B36.19/B36.10 standards, which provide tables specifying thickness based on size and pressure.
- Presssure : Pressure ratings are essential to consider. Elbows are designed for various pressures, indicated by ratings like 150#, 300#, or their PN equivalents. The specific pressure rating depends on the chosen material and the wall thickness.
- Angles : For changing flow direction, 45-degree and 90-degree elbows are the standard choices. Additionally, the radius of the curve greatly influences flow characteristics. Long Radius (LR) elbows provide a smoother transition minimizing flow disruption, while Short Radius (SR) elbows excel in tight spaces but create greater flow restriction.
- Types : Connection types vary depending on the application. Butt-welding is the most common for seamless pipe integration, and these often conform to ASME B16.9/B16.28 standards. For smaller sizes or specific needs, threaded, socket-weld, or flanged connections may also be available
- Superior Resistance to Corrosion : These elbows are engineered from materials specifically designed to combat corrosion. Stainless steel provides a baseline level of resistance, while duplex and super duplex grades are exceptional for seawater, acids, and other aggressive chemicals.
- Built to Last : High strength and excellent durability are hallmarks of these elbows, especially those made from duplex and super duplex alloys. They withstand demanding environments and mechanical stresses, ensuring reliable performance over time.
- Handling Pressure : Choose from a range of pressure ratings to match your system requirements. Elbows are designed to safely contain fluids and gases under various pressure conditions.
- Optimized Flow : Long Radius (LR) elbows promote smooth flow with minimal pressure drop, making them ideal for applications where flow efficiency is critical. Short Radius (SR) elbows excel when space is limited, even though they cause slightly more flow restriction.
- Wide Range of Applications : The corrosion resistance and adaptability of these elbows make them invaluable in numerous industries, including chemical processing, oil and gas, marine environments, and water treatment facilities.
- Easy Integration : Butt-weld connections are standard, providing a seamless and leak-proof connection with your piping system. However, it's important to ensure you use compatible welding techniques based on the chosen material grade.
- Quality Assurance : Adherence to ASTM, ASME, and other standards guarantees that these elbows meet dimensional requirements, material specifications, and overall performance expectations.
- Reduced Downtime : The combination of corrosion resistance, robust construction, and minimal maintenance requirements means your system experiences less downtime and maintains long-term cost-effectiveness
- Refinery & Petrochemical : Elbows in these industries redirect crude oil, refined products, and various chemicals throughout processing stages. They must withstand the corrosive nature of these fluids, especially sulfur-containing compounds.
- Chemical : These elbows are crucial for changing flow directions within complex chemical plant piping where acids, solvents, and other harsh chemicals are present. They're also found on storage tanks and in wastewater treatment systems handling corrosive substances.
- Oil & Gas : In the oil and gas industry, elbows redirect oil and gas flows for both onshore and subsea pipelines, often facing high pressures and corrosive fluids. They're also vital within processing equipment on platforms and refineries.
- Power Plant : Power plants use elbows in cooling systems, particularly those utilizing seawater, where corrosion is a major concern. They may also be used in lower-pressure steam lines and wastewater treatment systems, depending on the specific chemicals present.
- Offshore Platforms : Offshore platforms heavily rely on these elbows for various process systems handling corrosive fluids and gases. Super duplex grades are often chosen for seawater systems (like fire suppression and cooling) and for ballast control systems due to their exceptional corrosion resistance.
- Ship Building : Ships utilize these elbows in engine room piping for fuel, cooling, and exhaust. Ballast water systems demand saltwater-resistant materials. Specialized tankers may require various grades to handle corrosive cargoes.
- Industrial Machineries : Elbows find applications in industrial machinery where corrosive fluids are the hydraulic medium or when the machine's environment necessitates superior corrosion resistance. They are integrated into diverse process equipment and may be needed in washdown systems using harsh cleaning chemicals.
- Pharmaceuticals : The pharmaceutical industry demands clean, corrosion-resistant elbows for process piping, clean-in-place (CIP) systems, ingredient transfer, and purified water lines. They are also found in tanks, reactors, and other manufacturing equipment where purity is paramount.
- Pumps & Compressors : Elbows ensure smooth flow into and out of pumps and compressors, with LR elbows often used to reduce pressure losses. They might also be needed within cooling systems handling potentially corrosive fluids.
- Dairy & Food, Sugar Mills, Textile Machineries, Fertilizers & Pesticides : These industries prioritize hygienic design. Elbows need smooth, easily cleaned surfaces with resistance to both the products being processed and the cleaning solutions used to maintain sanitary conditions
Chemical Composition
Element | Percentage |
---|---|
Carbon (C) | 0.03% max |
Chromium (Cr) | 21-23% |
Nickel (Ni) | 4.5-6.5% |
Molybdenum (Mo) | 2.5-3.5% |
Manganese (Mn) | 2% max |
Silicon (Si) | 1% max |
Phosphorus (P) | 0.03% max |
Sulfur (S) | 0.02% max |
Nitrogen (N) | 0.08-0.2% |